|
 |
Zetpol¢ç  |
|
|
|
|
|
|
 |
|
 |
Zetpol¢ç (HNBR) ÀÇ ¼Ò°³ ¹× °³¿ä
|
 |
|
 |
|
»ê¾÷ºÐ¾ßÀÇ Á¾»çÀÚµéÀº ±Ý¼Óó·³ °Çϰí, ÇÃ¶ó½ºÆ½Ã³·³ °¡º¿ì¸é¼ ³»ÈÇмºÀÌ ÁÁÀ¸¸ç, °í¹«Ã³·³ ź¼ºÀÌ ÀÖ´Â "Metaplastomer"¶ó´Â ÀÌ»óÀûÀÎ ¹°ÁúÀ» »ý°¢ÇÏ°Ô µÇ¾ú½À´Ï´Ù.
ÀÚµ¿Â÷ »ê¾÷, ¿¡³ÊÁö »ê¾÷ ¹× ¿©·¯ ´Ù¸¥ »ê¾÷ºÐ¾ß °³¹ßÀÚµéÀº ¾î¶°ÇÑ »óȲ¿¡¼µµ ½Å·ÚÇÒ ¼ö ÀÖ°í ³»±¸¼ºÀÌ °ÇÑ "Metaplastomer"À» ¿À·£±â°£ ±â´Ù·Á ¿Ô½À´Ï´Ù.
Nippon ZeonÀº 25³â¿¡ °ÉÄ£ °í¹« »ç¾÷ÀÇ °æÇèÀ» ±â¹ÝÀ¸·Î "Metaplastomer"¿Í °¡Àå ±ÙÁ¢ÇÑ ¹°¼ºÀ» °¡Áø Elastomer, Zetpol¢ç¸¦ °³¹ßÇÏ¿´½À´Ï´Ù.
Zetpol¢çÀº ³»À¯¼ºÀÌ °ÇÑ °í¹«·Î °¡Àå ¹ü¿ëÀûÀ¸·Î ¾²¿©¿Ô´ø NBR¿¡ Ưº°ÇÑ ¼ö¼Ò÷°¡ °úÁ¤À» ÅëÇØ »ý¼ºµÇ¾ú½À´Ï´Ù.
¿©±â¿¡ ºÎ°¡ÀûÀ¸·Î Ź¿ùÇÑ ³»À¯¼º, NBRÀÇ ÀÛ¾÷ ¿ëÀ̼º, ³»¿¼º, ³»ÈÇмº ¹× ³»¿ÀÁ¸¼ºµîÀÇ ±â´ÉÀ» È®Àå½ÃŲ Á¦Ç°ÀÔ´Ï´Ù.
ÀϹÝÀûÀÎ ³»À¯ ¹× ³»¿¼º °í¹«¿Í ºñ±³ÇÏ¿© Zetpol¢çÀº ÀÎÀå·Â°ú ³»¸¶¸ð¼ºµîÀÇ ÈξÀ ¿ì¼öÇÕ´Ï´Ù.
Zetpol¢çÀº º§Æ®, ½Ç, ¿ÀÀÏ, È£½º, ·Ñ µîÀÇ H-NBR ºÐ¾ß¿¡¼ ¼±±¸ÀûÀÎ ¿ªÈ°À» Çϰí ÀÖ½À´Ï´Ù.
Zetpol¢çÀÇ »ç¿ëÀº ¿©·¯ºÐ¿¡°Ô °í¹« ºÐ¾ß¿¡¼ ½Å·Ú¼º°ú °ß°í¼ºÀ» Çâ»ó½ÃÄѵ帳´Ï´Ù.
|
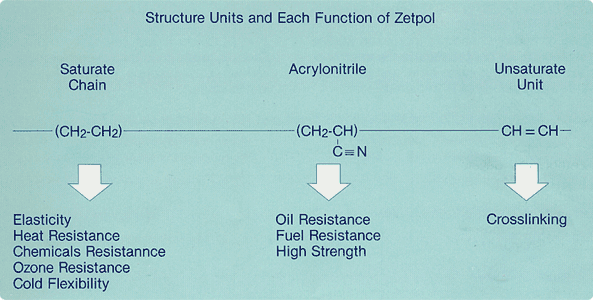 |
 |
 |
|
 |
Zetpol¢ç Grade Availabilities
|
 |
|
 |
|
Increase of acrylonitrile content improves Zetpol's oil resistance but reduces its low temperature resistance, just like NBR in general.
As its degree of hydrogenation is increased (iodine value is decreased), its heat resistance is improved, but creep increases at the same time, and its rubber elasticity at low tempreratures is impaired.
Zetpol is highly compatible with PVC. Blending it with PVC produces a material with greater oil and ozone resistances.
To enable you to put Zetpol to varous uses, Nippon Zeon is ready to offer several grades produced by various combinations of acrylonitrile content and iodine value.
|
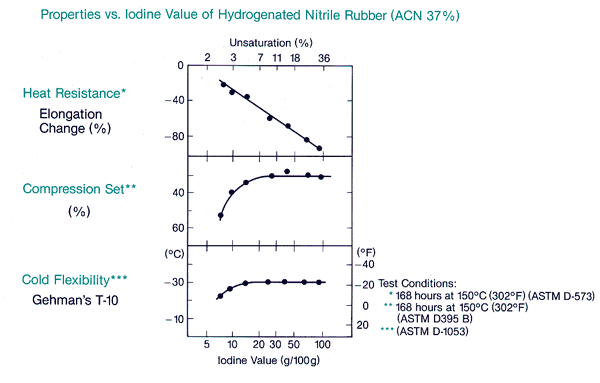 |
Grade |
Bound ACN (%) |
Iodine Value (g/100g) |
Mononey Viscosity (ML1+4100¡ÆC/212¡ÆF) |
Applications |
Zetpol 1020 |
44.0 |
25 |
78 |
Fuel hose, Fuel diaphragm, Feon packing, intank insulator |
Zetpol 1010 |
44.0 |
10 |
85 |
Zetpol 2020 |
36.0 |
28 |
78 |
Oil seals, Synchronous belt, Rolls, Oil hose, Drilling pipe protector |
Zetpol 2020L |
36.0 |
28 |
57.5 |
Zetpol 2010 |
36.0 |
11 |
85 |
O-rings, Packings, Gaskets, Oil seals, Oil hose, Well head seals, Blow out preventor, Water pump seal |
Zetpol 2010L |
36.0 |
11 |
57.5 |
Zetpol 2000 |
36.0 |
4 |
85 |
Zetpol 2000L |
36.0 |
4 |
65 |
PBZ-123 |
*44.0 |
*25 |
**48 |
PVC blend, Fuel hose, Fuel diapharagm,Intank insulators, etc |
*Base Zetpol **MS1+4100¡ÆC(212¡ÆF) |
|
 |
 |
|
 |
General Propreteis of Zetpol¢ç
|
 |
|
 |
|
Heat Resistance
Grades such as Zetpol¢ç 1020 and 2020 with iodine values of 20~30 when sulfur cured, can be continuously used for 1,000 hrs at 125¡ÆC(257¡ÆF).
On the other hand Zetpol¢ç 2000cured with peroxide can be continuously used for 1,000 hrs at 160¡ÆC(320¡ÆF)
| 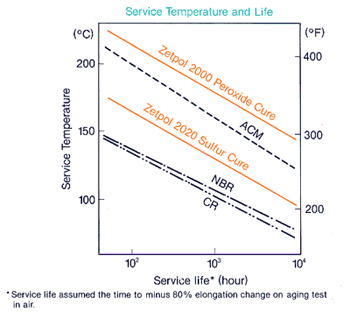 |
Oil Resistance and Brittle Temperature
With the same volume swell by oil, Zetpol¢ç shows a lower brittleness temperature than NBR 5~7¡ÆC(9~13¡ÆF)
| 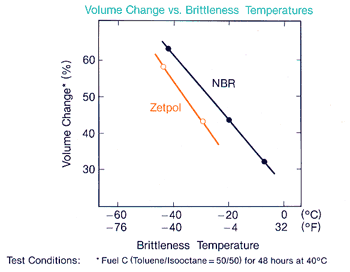 |
|
Tensile Properties
Zetpol¢ç has higher tensile strength and wear resistance then NBR, to say nothing of the conventional heat, and oil resistant elastomers.
|
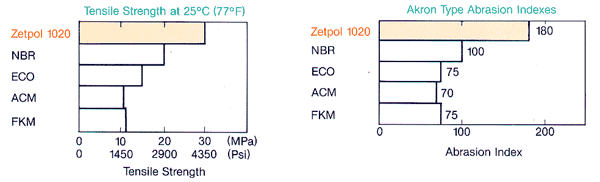 |
 |
 |
|
 |
Application To Automobile Fuel Parts
|
 |
|
 |
|
Zetpol, while retaining the gasoline resistance, of NBR shows about five times higher sour gasoline and ozone resistances than NBR.
Zetpol also has a lower birttle temperature than NBR displaying the same volume swell in gasoline.
Compared with fluorinated rubber and NBR, Zetpol satisfies a wider scope of the properties required for fuel parts applications and permits larger cost saving than FKM.
Accordingly, it is widely used for various fuel parts, including inner tubes of fuel hose which should assume a long service life.
Especially suitable for this application are Zetpol 1020, 1010, and their blends with PVC.
|
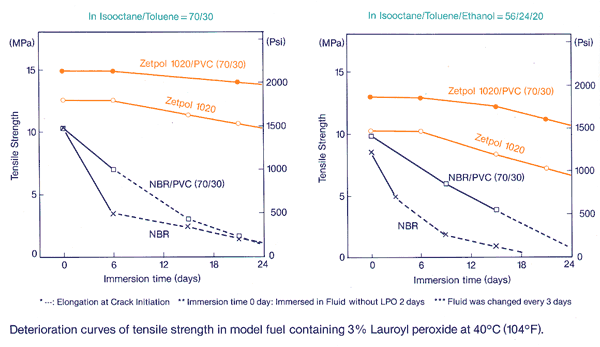 |
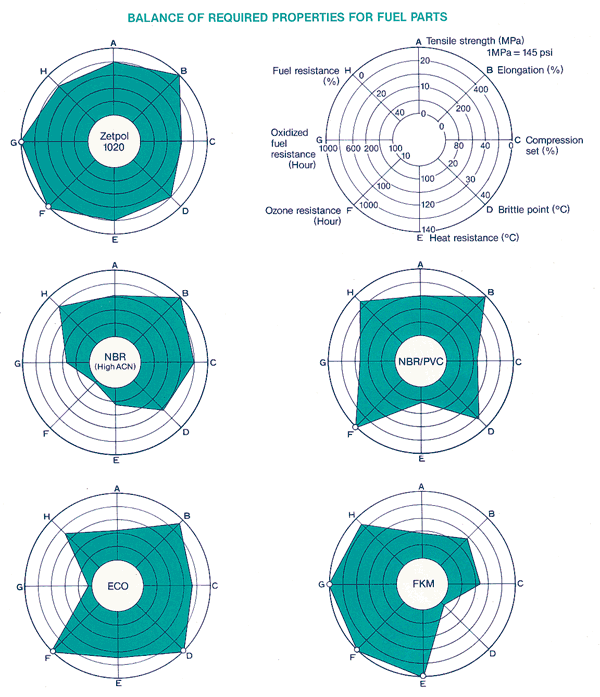 |
 |
|
Zetpol is a suitale material for use a belt applicatin due to its excellent tensile strength, wear- and ozone-resistance. it's has a heat resistance 30'C(54'F) higher then CR and therefore enables the manufacture of high-temperature belts not producible with CR.
Its temperature dependency of dynamic modules is small, so it is especially ideal for producing synchronous belts which must transmit force quite accurately over a wide range of temperatures.
Especially suitable for this application are sulfur cured Zetpol 2020 & 2020L.
|
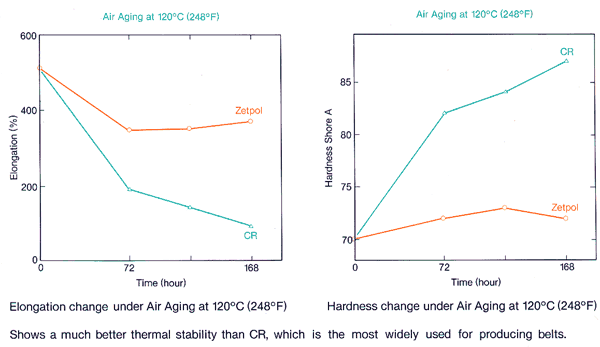 |
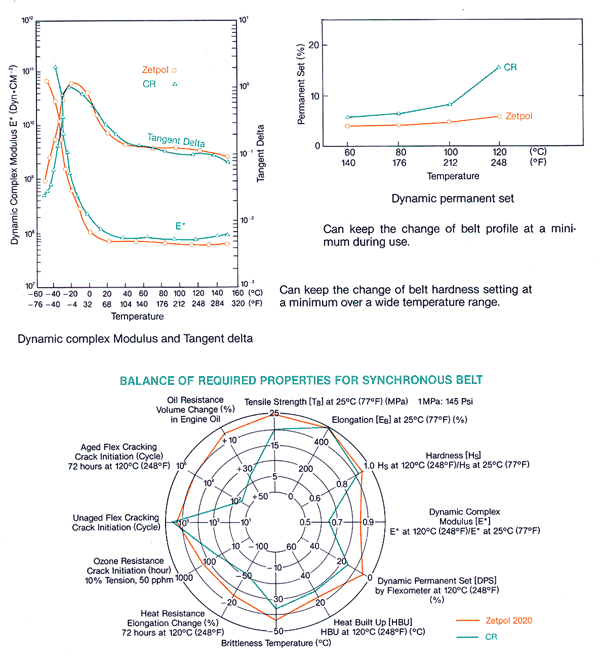 |
 |
 |
|
 |
Application To Oil Line Parts
|
 |
|
 |
|
Recently, long life lubricants are becoming common.
Several special additives in Tale1, some of which harm rubber materials, are added to these long life fluids.
Due to the popularization of long life oil, the deterioration of rubber by sour oil with metal sludge has come to be noted.
Zetpol shows little deterioration caused by these additives and sour oils.
It can also be designed with a high modulus and enormous tensile strength at high temperatures, making it ideal for use as a material for engine oil parts and hydraulic oil parts, as well as various kinds of oil hoses, oil seals, and packings.
Zetpol 2000, 2010, and 2020 are recommended for these applications.
|
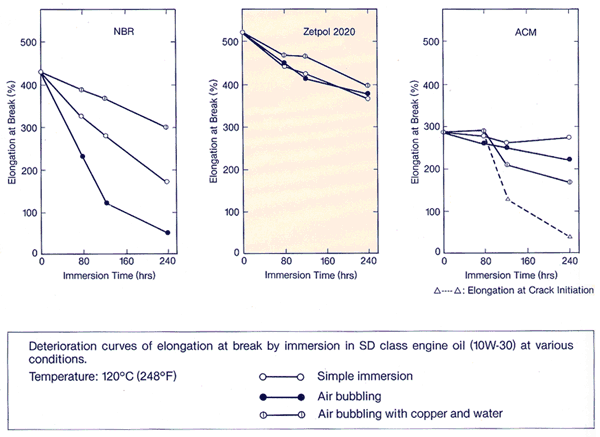 |
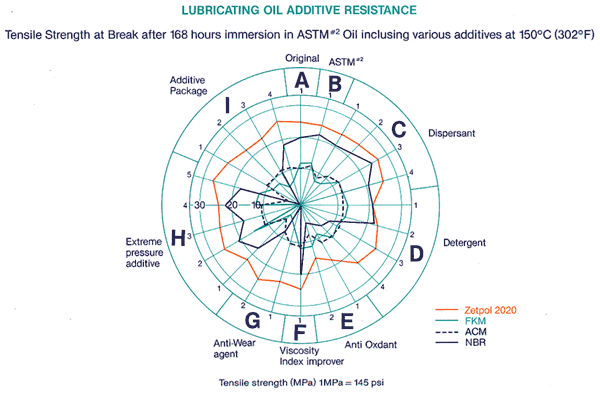 |
NBR is severely harmed by detergents, antioxidants and anti-wear agents.
ACM shows low tensile strength but is stable against the additives except alkyl phosphate and lead napthenate.
FKM shows low strength like ACM but is deteriorated by succinic-imide, sulfurized olefine and alkyl phosphate.
Zetpol is most stable, showing the highest tensile strength, against the additives but is changed slightly by zinc dithiophosphate.
|
Table 1 |
No. |
Type of Additive |
Main Chemical Composition |
Concentration* |
A-1 |
- |
Original tensile strength |
- |
B-1 |
- |
ASTM #2 oil with no additive |
- |
C-1 |
Dispersant |
Polyalkenyl succinimide |
10 |
C-2 |
Polyalkenyl succinimide/borate |
10 |
C-3 |
Polyalkenyl succinic ester |
10 |
C-4 |
Polyalkenyl succinimide/succinic ester |
10 |
D-1 |
Detergent |
Calcium sulfonate-Basicity 24 |
10 |
D-2 |
Calcium sulfonate-Basicity 300 |
10 |
D-3 |
Magnesium sulfonate-Basicity 400 |
10 |
D-4 |
Calcium phenate-Basicity 205 |
10 |
E-1 |
Antioxidant |
Primary dialkyl zinc dithiophosphate |
5 |
E-2 |
Secondaty dialkyl zinc dithiophosphate |
5 |
F-1 |
Viscosity index improver |
Polyalkyl methacrylate |
10 |
G-1 |
Anti-wear agent |
Olefin sulfide for gear oil |
10 |
G-2 |
Olefin sulfide (Technical grade) |
10 |
H-1 |
Extreme pressure additive |
Dialkyl phosphoric ester |
10 |
H-2 |
Dialkyl phosphoric ester |
2 |
H-3 |
Zinc dibutyl dithiocarbamate |
1 |
H-4 |
Molybdenum compound |
0.3 |
H-5 |
Lead naphthenate |
10 |
L-1 |
Additive package |
Package #1 for gear oil |
10 |
L-2 |
Package #2 for gear oil |
10 |
L-3 |
Package for automobile engine oil |
10 |
L-4 |
Package for ATF (Dexiron IID) oil |
10 |
*gram/100cc of ASTM #2 oil |
|
 |
|
With the increase of deep oil-wells, rubber materials with resistances to heat, hydrogen sulfide, corrosion inhibitor, steam and blister besides oil resistance have come to be strongly required.
Zetpol meets all these requirements, and also shows easy adhesion to metals and enormous tensile strength, making it an ideal material for blowout preventor, pipe protector, well head sealing, packing and other parts for oil wells.
Zetpol 2000,2010, and 2020 are normally used for these applications.
|
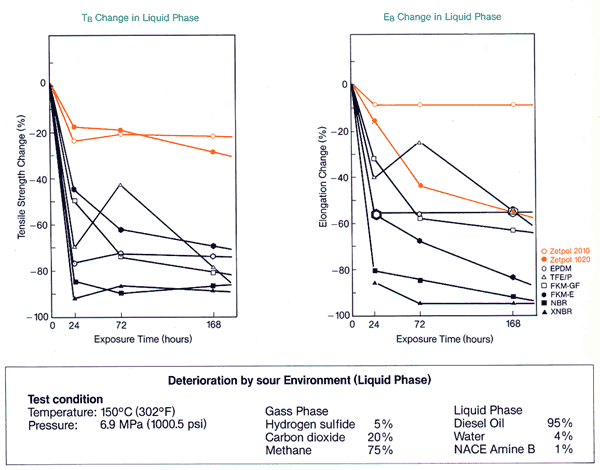 |
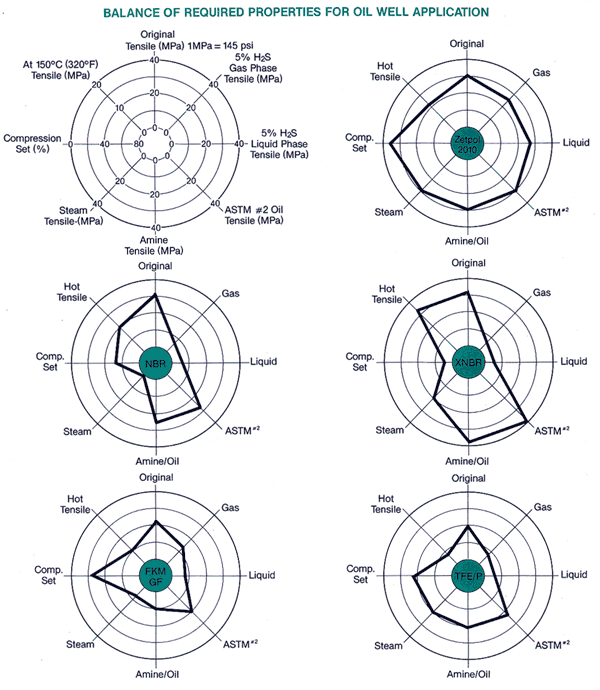 |
 |
|
In addition to displaying oil resistance comparable to that of NBR, Zetpol has an excellent resistance against chemicals, steam, wear, and heat.
Accordingly, it is ideal for industrial products normally made of NBR, such as various kinds of industrial rolls, including iron rolls and printing rolls, and various kinds of O-ring, packing, and gaskets.
These Zetpol products can be used under severest conditions and with much longer service life expectancies.
In addition, the processing method of Zetpol is fundamentally the same as that normally applied to NBR, so nosecial facilities are required.
|
NBR is severely harmed by detergents, antioxidants and anti-wear agents.
ACM shows low tensile strength but is stable against the additives except alkyl phosphate and lead napthenate.
FKM shows low strength like ACM but is deteriorated by succinic-imide, sulfurized olefine and alkyl phosphate.
Zetpol is most stable, showing the highest tensile strength, against the additives but is changed slightly by zinc dithiophosphate.
|
Steam Registance of Zetpol 2000 |
Immersion time (hours) |
150¡ÆC/302¡ÆF |
175¡ÆC/347¡ÆF |
TB change (%) |
EB change (%) |
HS change (points) |
TB change (%) |
EB change (%) |
HS change (points) |
72 |
+9 |
-5 |
-1 |
+5 |
+5 |
-1 |
240 |
¡¾0 |
¡¾5 |
-1 |
- |
- |
- |
480 |
-3 |
+5 |
+1 |
+4 |
+11 |
¡¾0 |
960 |
+1 |
¡¾0 |
-0 |
¡¾15 |
-5 |
+4 |
|
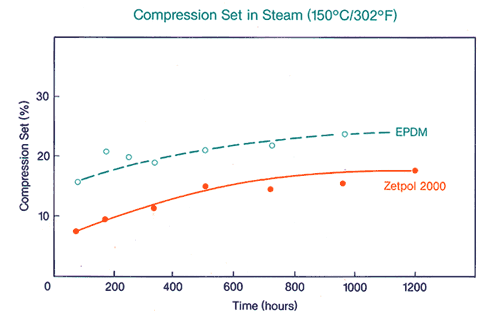 |
 |
|
|
|